Hallo,
weiter gehts mit Selene 😉
Die Älteren werden sich erinnern – ich habe damals auf Dominika ein paar Außenbordmotoren auf dem Vordeck repariert. Schon dort ist mir aufgefallen, daß das Deck im Bereich der Schottabdecking weich wird. Trotz der monsunartigen Regenfälle blieb das Boot innen jedoch trocken. Mir war klar, daß eine Reparatur in der Karibik kompliziert, teuer und sicher auch ein Stück weit Pfusch wird. Letzteres, da ich sicherlich nicht das passende Harz, Gelege und vor allem Füllmaterial bekommen hätte.
Neptun hat auf der Rückfahrt mal gezeigt, was so geht und kubikmeterweise Wasser übers Deck laufenlassen. Im Bereich der Küche und im hinteren Bereich des Salons tropfte seit dem immer etwas Wasser von der Decke. Mittlerweile passiert das auch, wenn es mal etwas stärker regnet…
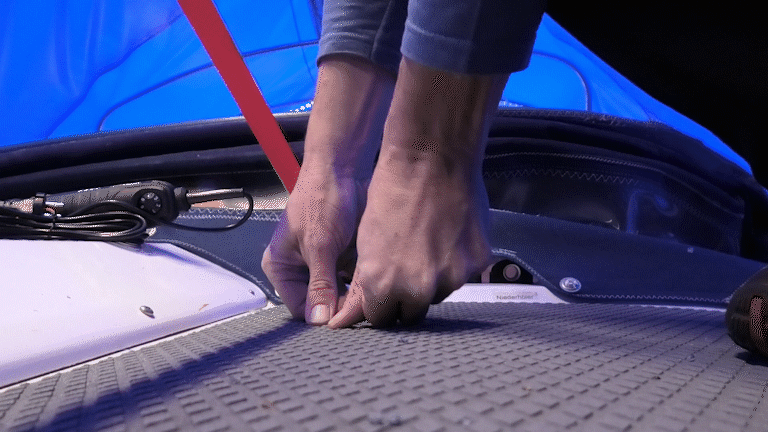
Ich habe mich lange um diese Arbeit gedrückt. Im vorherigen Lager wäre dies auch sehr schwierig umsetzbar gewesen. Dieses Dilemma hatte ich bereits in einem meiner älteren Beiträge erklärt.
Dank der neuen Persenning und dem unkomplizierten Zugang zum Boot kann ich nun an jedem Tag und bei jedem Wetter am Deck arbeiten. Dank der globalen Erwärmung geht das auch im Oktober/November 😉
Das ist sicher der schwierigste Moment: Der erste Schnitt ins unversehrte Deck. Auch wenn es nicht so aussieht: Es ist defekt…
Das war abzusehen: Das Balsa ist verrottet und voller Wasser.
Nun ist die Frage: Wie großflächig ist der Schaden? Über Klopfen ist das kaum herauszubekommen, da das Deck in dem Bereich zu inhomogen ist. Ich stecke einfach einen Schraubendreher in das weiche Balsa und arbeite mich Stück für Stück voran.
Wie man auf diesem Bild sieht, gibt es Stellen, wo der Verbund noch sehr stabil ist. An anderen ist das Balsa leicht feucht, das GFK hält jedoch noch. Der größte Teil besteht jedoch aus einer Art Humus, in dem man Kartoffeln pflanzen möchte.
Das ist übrigens auch der Grund, warum ich keine große Platte heraussägen konnte. An manchen Stellen war der Verbund so fest, daß das GFK kaputt gegangen ist, bevor das Balsa oder die Klebeverbindung aufgegeben hat.
Die meiste Feuchtigkeit befand sich im Bereich des Fensters und der Schottabdeckung.
Da hat jemand normale Dübel benutzt, um die Abdeckung aufzuschrauben…
Steuerbordseitig fand ich im Bereich der Kassette des Fensters jede Menge Silikon – und zwar zwischen Ober- und Unterschale des Decks. Eine Begutachtung vom Salon aus zeigte folgendes:
Da hat jemand 2 Löcher gebohrt und Silikon eingedrückt. Anscheinend war das Fenster mal undicht? Wenn das Deck fertig ist, habe ich vor das Fenster mal neu einzudichten. Das ist – wie sollte es anders sein – auch mit viel Silikon eingesetzt.
Zum Schluß habe ich gut 2m² des Decks aufgesägt. Leider wollte meine Kamera von heute auf morgen den originalen Akku nicht mehr erkennen. Den originalen Ersatzakku übrigens auch nicht…
Damit war das Wochenende schon wieder vorbei und eigentlich sollte der Blogbeitrag folgen. Ich hatte wieder meine übliche Liste erstellt und mich an die Bestellung gemacht. Die Lieferung erfolgte sehr schnell und der Wetterbericht sagte für das kommende Wochenende traumhafte Temperaturen voraus. Dazu war der Montag noch Feiertag.
Also, auf an zur Küste und weitermachen!
Erste Amtshandlung: Deckenpaneele entfernen.
Als nächstes ging es ans Schleifen der zu klebenden Flächen. Damit das nicht zu staubig wird habe ich mir einen Adapter für meinen Staubsauger gedruckt.
Es gibt mehrere Möglichkeiten, wie man an das vorhandene Material an-laminieren kann. Ich habe mich in meinem Fall dazu entschieden eine Phase anzuschleifen. Das geht mit einem kleinen Bandschleifer recht einfach.
Nun ging es ans Auffüllen. Ich hätte auch wieder Balsa genommen – immerhin hat es über 40 Jahre gehalten – aber nach einigen Recherchen bin ich auf Mycell/Airex Platten gestoßen. Im Video rede ich glaub ich von Faserplatten: Das ist natürlich falsch. Den Fußboden im Cockpit werde ich auch noch mal aufsägen. An dieser Stelle hatte ich Styrodur verwendet. Davon würde ich mittlerweile abraten, da der Verbund nicht stabil genug, bzw. das Styrodur zu weich ist.
Auf gehts! Ich erstelle ein Deckpuzzle 😉
Die Airex Platten sind sehr stabil und steif. Damit sich das Ganze schön ans Deck anschmiegen kann, werden die Platten auf der Rückseite geschlitzt.
Das Puzzle zu erstellen war sehr aufwendig. Da die Platten unter die Kassetten von Fenster und Luk geschoben werden müssen, mußte ich mir eine Art Reihenfolge einfallen lassen, damit das Ganze später überhaupt verklebbar ist. Dazu kommt, daß das Balsa 18mm stark ist, es aber die Airex Platte nur in 16 oder 20mm gibt. Damit lief der Schleifer sehr oft 😉
Ein paar Stunden später:
Die untere Deckschale hat viele Löcher, die ich alle zugeklebt habe. Die Plane ist dafür, falls ich doch eins vergessen habe.
Los gehts! Zuerst alle Ecken und Kanten per Pinsel, wo ich später mit der Rolle nicht hin komme.
Es folgen die Flächen. Als Harz habe ich mich für Epoxydharz L und Härter GL2 entschieden. Sicherlich gibt es auch günstigere Harze, aber die Kombination hat eine Zulassung vom germanischen Lloyd für den Bau von Booten und Rotorblättern für Windkraftanlagen. Der Härter hat eine sehr lange Tropfzeit von 210 Minuten (bei Ansatzmenge von 100ml pro Gang).
Die erste Runde mit dem Harz dient nur dazu, daß das Ganze nicht zu trocken wird. Um gescheit kleben zu können wird das Harz im nächsten Gang mit Baumwollflocken angedickt und mit einer Zahnspachtel aufgezogen.
Auch die Airexplatten bekommen eine Salbung mit reinem Exoxydharz.
Die Löcher in den Platten dienen zum späteren Vergießen. Die untere Deckschale ist nicht so plan, daß die Platten vollflächig aufliegen werden.
An einigen Stellen mußte ich ganz schön grübeln, wie es wieder zusammenkommt. Glücklicherweise habe ich alles ordentlich mit Strichen markiert und jedes Teil numeriert.
Im mittleren Teil ist das Deck leider etwas abgesackt und der Airex Schaum lag nicht an der Kassette vom Fenster an. Um das zu beheben habe ich das Deck von unten etwas ausgesteift. Zum Belasten wären Sandsäcke eigentlich am besten geeignet. Da ich keine zur Hand hatte, wurde alles verwendet, was Gewicht hat 🙂
Am nächsten Tag, ein Montag, ein Feiertag, mußte der Schleifer für gut 2 Stunden eingesetzt werden. Von den Platten mußten noch 2 mm abgeschliffen werden. Mit einem Stahllineal prüfe ich, ob schon genug Platz für das Laminat da ist.
Im nächsten Schritt mußten sämtliche Löcher, Fugen und Spalten gefüllt werden. Das Harz muß dazu gut fließen können. Man könnte pures Harz nehmen, jedoch trägt dieses mit einem Füllstoff besser. Mit Baumwollfasern wird das Ganze zu schnell pastös, weshalb Micro-Balls eine Lösung sind. Micro-Balls sind etwa 75 µm große Hohlkugeln aus Bor-Silikat-Glas und wiegen gerade mal 0,19 g/cm³. Der 5l Eimer, den ich gekauft habe, wiegt gerade mal um die 600 g.
Dabei sollte man sich etwas Zeit nehmen. Durch einige Löcher konnte ich recht viel Harz einfüllen.
Der nächste Schritt ist das Laminieren des Geleges. Ich nutze ein biaxiales Gelege mit einem Flächengewicht von 450 g/m². Man sollte für solche Arbeiten unbedingt ein Gelege (und kein Gewebe) nutzen, da dieses höher belastet werden kann.
Wie schon gesagt: Es gibt mehrere Möglichkeiten das zu laminieren. Ich habe mich dazu entschieden 2 Lagen genau passend zu machen und eine mit einem Überlapp von etwa 1,5 cm zu laminieren.
Um den Stoß stabiler zu machen, kommt an diese Stelle ein Gewebeband mit einem Flächengewicht von 160 g/m³ zum Einsatz. Fürs erste nur eine Lage – falls das zu wenig ist, kann ich später noch etwas aufbauen.
Letzter Schritt eines sehr langen Tages ist das Aufbringen von Abreißgewebe. Viele nutzen das, weil man darauf sofort wieder laminieren kann (also ohne Schleifen). Ich nutze es, um überflüssiges Harz aus dem Verbund zu bekommen. Das Harz bringt nur Gewicht und keine Stabilität. Diese kommt nur aus den Gelegematten.
Die Nacht war recht frisch und das Harz am nächsten Tag leider noch nicht sonderlich fest. Ich hatte nur keine Zeit mehr und das Abreißgewebe mußte runter. Ich muß das Ganze sowieso noch Schleifen und Füllern. Vielleicht muß ich an einigen Stellen auch noch etwas Gelege laminieren, falls die Spachtel zu dick wäre. Von daher ist mir das „Finish“ recht gleich.
So! Das soll es erst mal gewesen sein. Ich habe bereits alles da, um weiterzumachen. Fortsetzung folgt – hoffentlich bald 😉
So long,
Martin
Video:
Hi Martin.
Tolle Arbeit.
Aber das du Epoxy ohne Atemschutz verarbeitest, hat mich doch gewundert.
Schöne Grüße aus Solingen Christian
Moin Christian,
das Epoxy und der Härter sind völlig geruchlos und lösen auch nichts an. Der Härter ist ätzend – da wäre eher eine Schutzbrille wichtiger 😉 Das ist auch der Grund, warum ich auf reas (recht teure) Schiffsbauharz gegangen bin.
Du hast aber recht – es gibt Harz/Härter Kombinationen die bestialisch nach irgend einem Lösungsmittel stinken 🙂 Diese lösen dann auch das Füllmaterial an.
I’m going to have to take my time reading this though it relates directly to my boat as well (and many boats by guess)…
I have a few soft or slight ‚give‘ points on my deck…
The caveat is the deck was not manufactured using Balsa but instead a so-called cross-laced inorganic foam…
Should I be worried nonetheless…?
Hallo Martin,
das ist ja mal wieder eine präziese Anleitung von dir – danke dafür! Ich drücke die Daumen für gutes Laminierwetter.
Lieben Gruß aus dem Laminierparadies Griechenland von Bord der Mokendeist, Stefan
https://mokendeistsegeln.wordpress.com/